A development and study of a holding furnace based on technical specifications

Aluminium holding furnace technical specifications:
Casted parts: 25kg
Dipping system: 35kg ladle
Filling system: 600kg transfer ladles
Holding capacity: 3000kg
Max Metal T°C: 700°C
Working T°C: between 650°C and 680°C
Dipping level adjustable
Challenges:
Easy communication with other equipment
Easy communication with operators
Easy cleaning of the bath and the whole furnace, without removing the heating system
T°C regulation +/- 2°C
High Aluminum Quality
Low electrical consumption
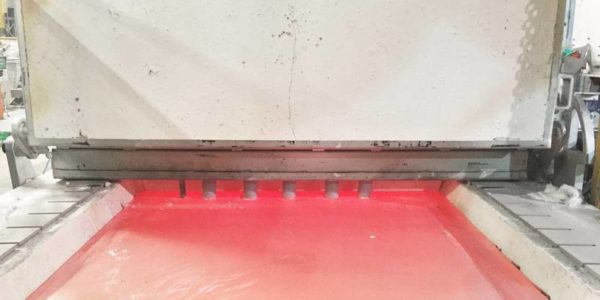
Our solutions for temperature holding furnace:
Lethiguel, LH3000 – Holding Furnace
Capacity: 3000kg
Working capacity: 1300kg
Heating system: 3x15kW immersion heaters
Regulation system: SIEMENS PLC S7-1500, PID / PFC regulation loop
HMI: SIEMENS TP 12’’
Tower lights for aluminum level + Tower lights for process status
Adjustable feet
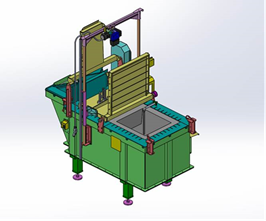
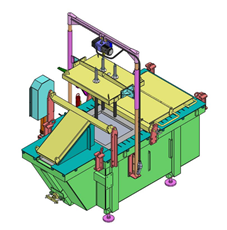
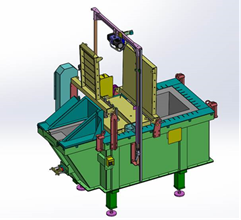
Results:
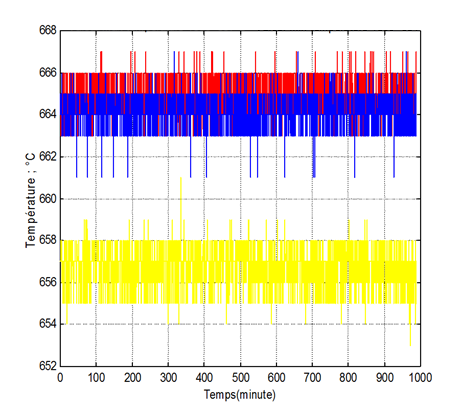
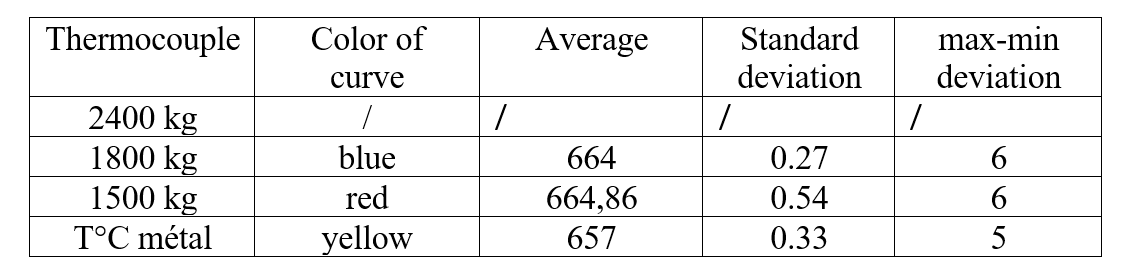
The average variation is around 0.54°C and small variations (up to 6°C) occurs when the furnace is being filled. To prevent this variation it is highly recommended to fill the furnace with aluminum at the same holding temperature. The regulation objective is fulfilled with our system.
Energy consumption and temperature raise.
The furnace consumes around 18kW to hold a 680°C temperature when it is full. The extra 27kW installed can then be used to raise the temperature at 25-30°C/h (3000kg) or 40°C/h (2100kg).
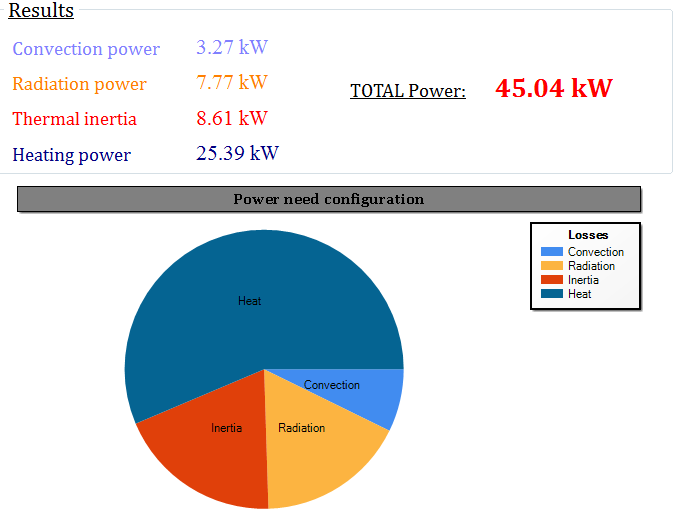
An “Eco mode” is installed to lower energy consumption during production stop. The energy saving is around 150kWh for a complete weekend stop.