Jet Cooling is a technology that is dedicated to handling hotspots. Thanks to high pressure capacity and sequential cooling, it enables leveling the die temperature and removing any hot area by reaching core pins and inserts, preventing porosity and shrinkage problems.
A case study in Jet Cooling Technology
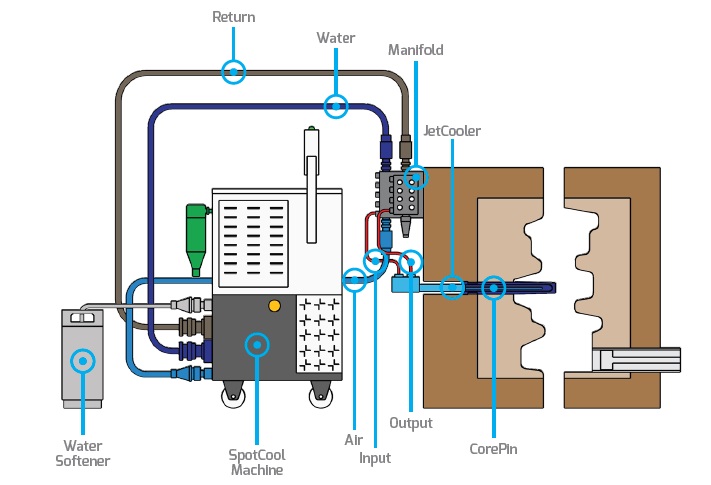
Cooling hot spots for a crank case
The use of thermal cameras allow us to point out the efficiency of the cooling in the core pins A and B. These pictures are taken before the spray-cooling phase. The result is a drop of 150°C in the core pins. Furthermore, all the zone around the core pins equipped with jet cooling also benefits from the cooling impact, a drop of 70°C.
The cooling times lasts 10 to 15 seconds.
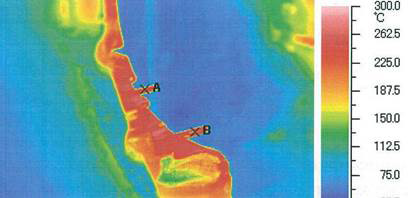
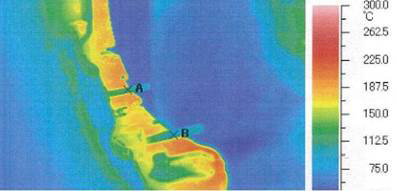
The reason why you should use Jet Cooling in casting
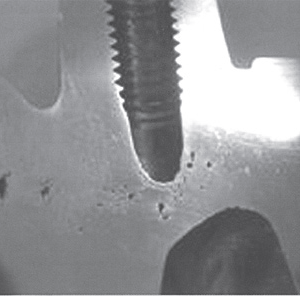
Casting without the use of jet cooling technology: Porosity occurs near thread
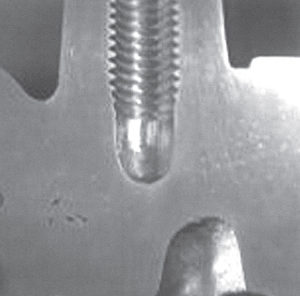
Casting when using jet cooling technology: Decreased porosity

Chill zone without the use of jet cooling technology
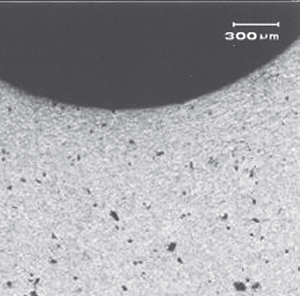
Chill zone with the use of jet cooling technology for 10 seconds