One of a cast house reached out to us for an issue that they have been facing for quite some times. A temperature drop in launder of a gravity die-casting department, on the H-line. The temperature is low in the launder between the first holding furnace and a second holding furnace where the aluminum is poured.
A case study in a gravity die-casting industry
Problem encountered by the die-casting house:
High power consumption
Low productivity
Low aluminum quality
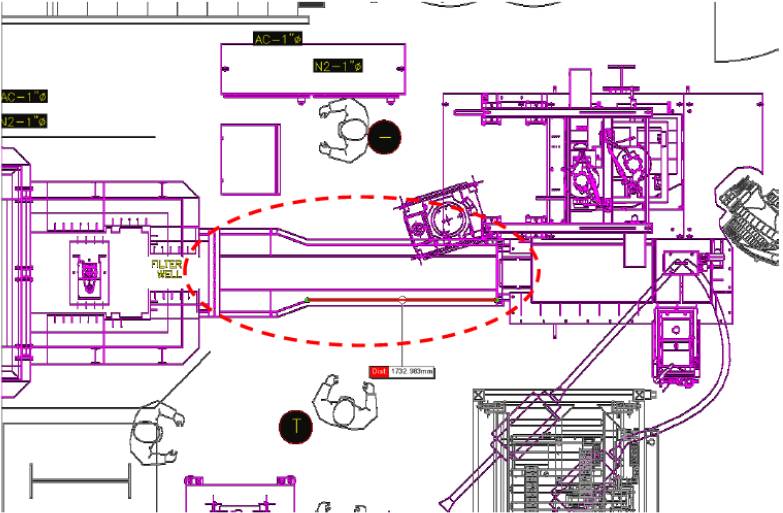
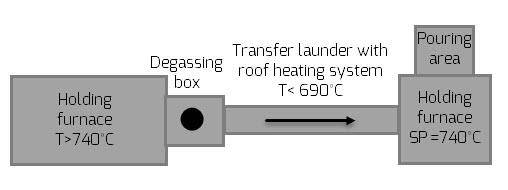
Initial launder’s specifications:
A roof heating system
32 kW radiation
Closed lids
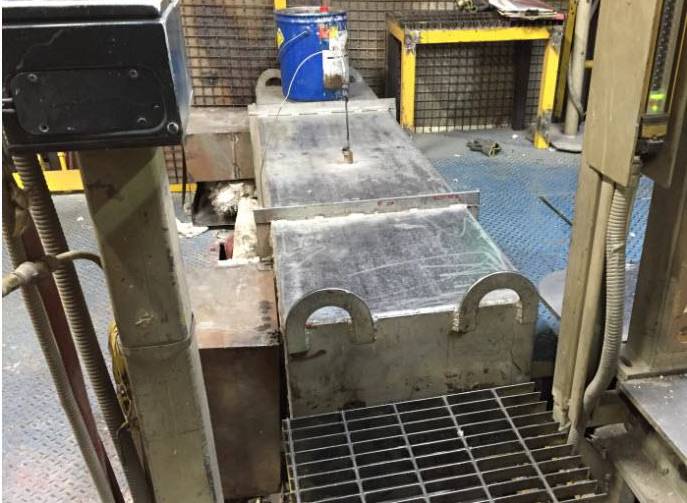
Challenges for the aluminum handling in the launder:
The aluminum temperature in launder: 611°C
The roof heating system was not able to maintain nor improve the temperature they wanted to have in the launder (from 735°C up to 780°C).
The aluminum had to spend more time in the second furnace in order to reach the right temperature in order to cast quality parts.
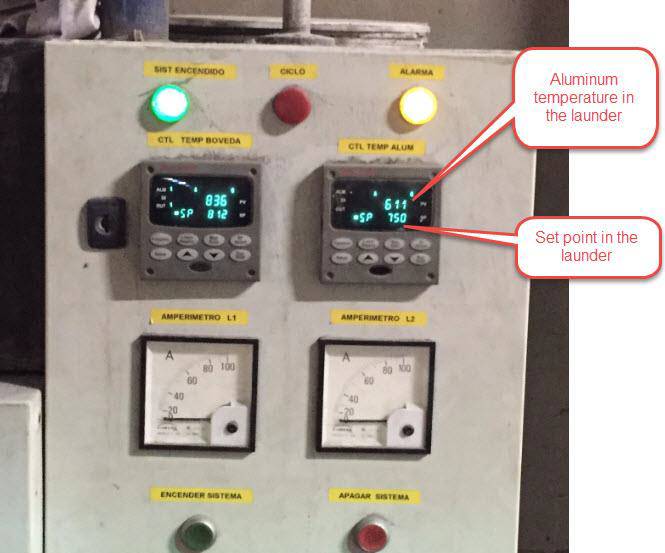
Our solutions for aluminium temperature holding:
2 L-type heaters of 8kW each
New lid for the launder
An electrical cabinet to regulate the L-type heaters.
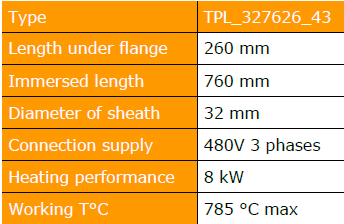

Results for the aluminium die-casting temperature:
By providing 16kW, we are able to reach the right temperature.
You might be interested